In today’s modern workshops most companies are still reliant on a crosscut saw design that has been in use since machinery began to turn. Either a Radial Arm or a heavy duty crosscut saw that rely on the man pulling the saw over the timber with the dangers that brings. The Health and Safety executive must wonder why this machine is still being used in the 21st Century.
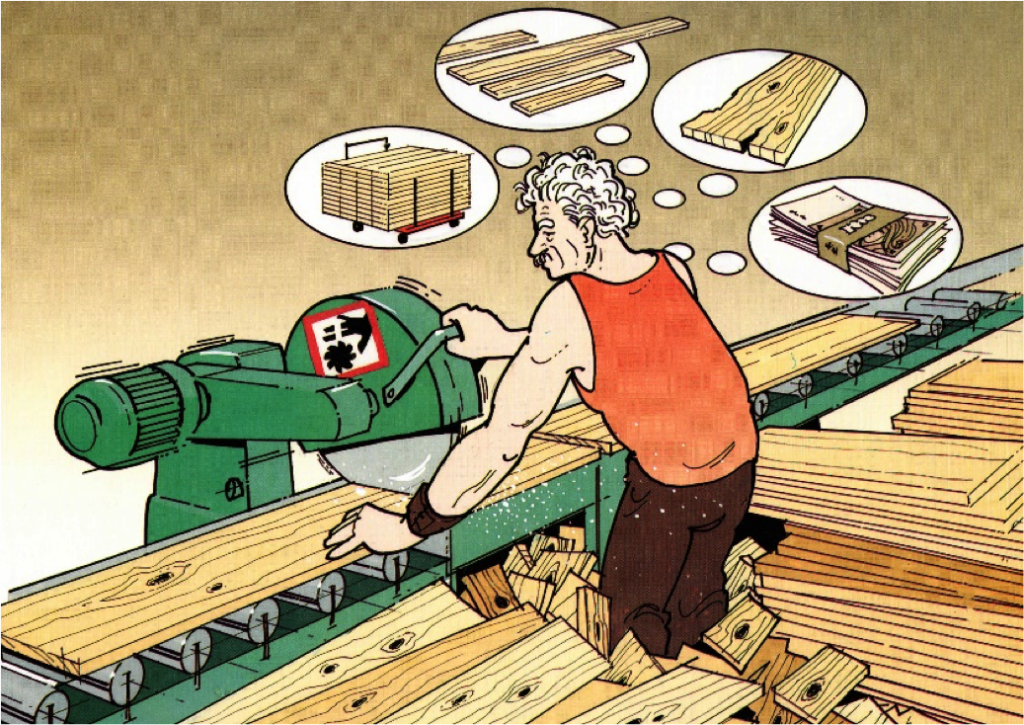
Our man on the crosscut seems to have a job that is dead simple. Look at the cutting list, set up an end stop or two, slide the board to the stop, and cut.
BUT IS CROSSCUTTING REALLY THAT SIMPLE?
Well I guess it is! We have done it that way for years.
However, if a company wants to get the best yield out of his expensive timber and save the time of that costly employee, we must look for a different solution that will make more money for you!
At present the crosscut man needs to have a brain like Einstein.
Where’s my list? What are the different lengths I require? What timber length am I taking it from? Has it got splits at the end? What knots are in the way? Is this the best cut length I can achieve? Jeeps this is heavy! Now I have cut the length what pallet do I put the parts on?
And at the same time the job takes twice as long for this man who uses his skills so readily on AN-OTHER machine! He has simply too many questions to answer to even think is he cutting the best for the company!
Let’s consider another way…… A Dimter Unicut P / Opticut S50
A saw that will push the timber into the cutting zone and at the same time work out the best cutting option to get the best yield / value from the material.
We must consider where he gets his information from (the cutting list) and how he is going to deal with a cut length. But the operator, in essence just has to load the saw. The cutting list can be uploaded direct from the office PC or by a “usb” stick inserted into the saw control panel.
The operator picks up a board. The start button is pressed, and the board is fully optimised from the cutting list and essentially the operator stacks the boards at the far end. Simple…..
But what if multiple cutting lists are cut? It would be suggested that a method of organisation after the saw be used to understand what has been cut. Possibly a simple label applied by the operator to the end of the timber, or a visual aid to advise what has been cut and who the job is for! A crayon marking the board.
In fact, the more cutting lists the better the timber yield! The many more component lengths increasing the optimization for the system, and speed of the overall process.
Very little pushing and sliding by the operator, loads of time to think about, the product!


The Benefits
- 50% less time to cut the material
- Optimised material could save up to 10% of the yield
- Operator released to run further operations!
- Consistent high quality with predictable production results.
- Far safer operation.
- Information for further machine operations.
If £250,000 of stock were crosscut each year a saving on yield could be £25,000 a year.
The savings on timber alone could pay for the Saw in under two Years! And that’s without time saved by the operator!
See Unicut P video below:
Find out more today:
If you want to find out how to make money when cross cutting, Click here!
Or feel free to connect on mobile 07836 704691!